Rota-Rack® Parts Accumulator
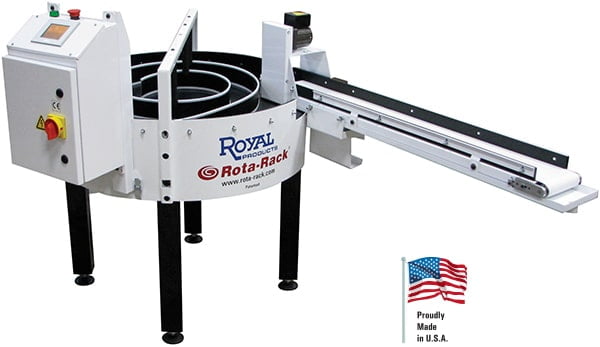
Do you know
- There are 168 production hours in a week.
- You are probably only using 40 of them.
- Your machines are worth $100 per hour.
- You could be making an extra $12,800 per week on each machine with a Rota-Rack®.
- You already invested in the bar feeder – how can you not complete the automation package?
- Pays for itself in less than two weeks - Incredible!
- What are you waiting for?
The patented Royal Rota-Rack® is an automatic accumulator that can be used with any bar-fed CNC lathe to safely collect finished parts, providing hours of highly profitable, unmanned production.
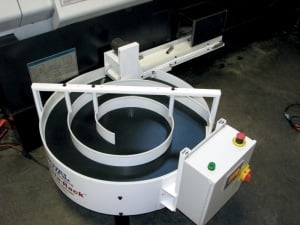
5 PM – Tuesday
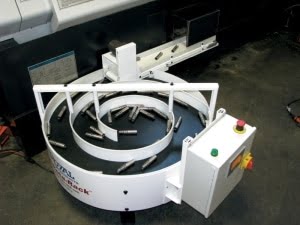
11 PM – Tuesday

6 AM – Wednesday
Big Benefit #1
Increases Capacity, Throughput, and Profits
- Run existing machines extra hours: nights, weekends, lunch breaks, etc.
- Faster cycle times – no waiting for an operator to unload parts / empty collection boxes.
- Higher efficiency – produce more parts per shift.
- Better employee utilization – why have a person do a job that can be handled with simple automation?
- Increased profitability.
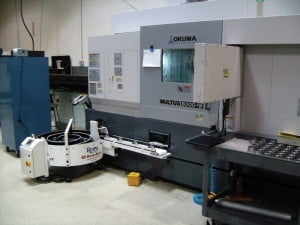
Big Benefit #2
Eliminates Part Damage
The Royal Rota-Rack® has been designed to provide maximum part protection, a feature that is important for all parts but one that is especially useful for parts with delicate external features like threads, edges, and corners.
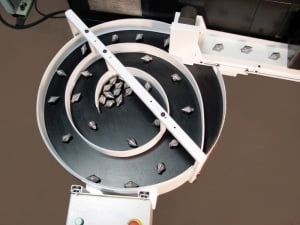
- Each time the Rota-Rack® collects a finished part, the turntable smoothly rotates to the next position to ensure that the following part will not forcefully collide with any of the previously-collected parts.
- All contact surfaces of the Royal Rota-Rack® and conveyor are covered with a high-lubricity UHMW plastic material to minimize friction and protect surface finishes.
- Reducing scrap and rework costs directly improves profitability.
- The Rota-Rack’s® unique spiral helps keep finished parts in sequential order, aiding quality control by enabling first piece/last piece inspection.
Big Benefit #3
Provides Complete Reliability
The Royal Rota-Rack® won’t show up late, doesn’t get sick, and keeps working long after your last employee leaves for the night or weekend.
First day of hunting season? Big snow storm? Cousin's wedding? The Rota-Rack® doesn’t care. How many of your competitors will be turning out parts
on Super Bowl Sunday?
The Heavy-Duty Royal Rota-Rack® is Available with Three Conveyor Options:
- The deluxe control enables the Rota-Rack’s® operation to be matched to the machining cycle time.
- Three inputs are entered by the user: part cycle time, amount of rotation, and auto-shutoff quantity.
- With this control, each time a part drops out of the machine, the Rota-Rack® will energize and index.
- The deluxe control is useful for applications where accurate spacing is required to prevent delicate parts from coming into contact with each other.
- “For rare applications where a user may want the Rota-Rack® to be tied into the machine tool control (not recommended), a special “Integrator” control box is available. Contact us for details.”
- There are three conveyor options to handle all clearance needs.
- The conveyor bolts to the Rota-Rack and plugs directly into the control.
- Long conveyor includes a support leg.
Rota-Rack®
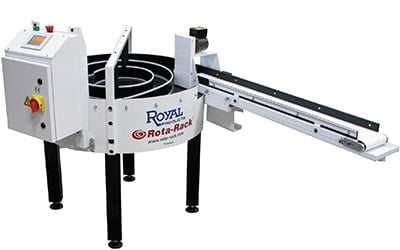
Optional Conveyor

Royal Heavy-Duty Rota-Rack®
PRODUCT | PART NUMBER | PRICE | |
---|---|---|---|
Heavy-Duty Rota-Rack™ with Deluxe Control | $14,955.00 |